This note like my other one on coaxial cables has been marinating since late May, 2020. As part of my boat network upgrade I wanted to add a remote microphone to my helm while moving the radio head unit below deck into my navigation system. The connectors for the remote mic cable were too large to pass through my Pedestal Guard holes and numerous other tight passages, so I elected to cut the cable and splice it back together. The cord connecting the remote microphone to the radio head unit consists of seven wires, with one of the seven being a tiny coaxial cable with an external shield layer, so effectively an 8th wire.
As with a majority of my projects, I can refer back to Sensei Williams’s experience doing similar/the same thing before me. Upgrading electronics on Thelonious II, he was required to cut his SeatalkNG network cable. He spliced the cable back together with a wee bus bar. Then a more knowledgeable local yacht electrician suggested he could have used “plug-in connectors.”
“That’s the ticket!” I thought. “I’m a clever guy – I’ll learn from others’ challenges.” So I went googling for a push-in connector. For you know, like infinitesimally small wires. I think they are 26 gauge. I really didn’t find very much for tiny tiny push in connectors. I ordered this connector on-line:
It was way too big and meant to accommodate much larger wires. I sent it back.
I thought again. “I can’t be the only person solving this problem. What about radar cords and stuff?” I googled harder.
I came up with this Airmar/Gememco connector from Defender and I ordered one:
Good times. You just screw the wires into either side, and boom, connection made. It comes with its own 1.3mm allen wrench. Perfect.
Day 1: The point I chose to sever the cable was under my helm, inside of my quarterberth. So I would be working on my back in the dark. At least I had a mattress to lay on.
One has to remove the insulation from around the tiny wire before one can splice it. I tried to use my standard wire strippers. The smallest diameter hole is 22awg and so it did not work very well. I tried to use a razor blade and wound up cutting most of the wires in half. But I carried on! I wanted to try my wire splicer and make my remote mic work!
The connector relies on set screws that are tightened with the included, as I mentioned 1.3mm allen wrench. You can see the splice connector dangling near the blue tape:
You know what’s great about working with a 1.3mm allen wrench? Nothing. Not a gosh darn thing. You’re already trying to fit these wispy wires into a tiny hole in the dark upside down, but then you have about 2.5 twists of the tiny set screw with the tiny wrench to try to make the connection. Then when you’re done, it seems like if you sneeze the thing will blow apart. Push in connectors, my foot!
Day 2: So there has to be a better way to strip wires than by trying not to slice through them with a razor blade. Let’s refer to the University of YouTube.
Ah hah! Here’s a good solution:
https://www.youtube.com/embed/n5o2drU65UM?wmode=opaque&start=36
That looked great! Awesome! You just light the tip of the insulation on fire and then pull it off. Totally makes sense! Great idea. (And somewhere in the back of your mind, you’re thinking “Huh, grabbing flaming plastic with your fingers. Is that a smart thing to do? Does that hurt a little?”)
So anyway, let’s try it in the boat.
The answer is, yes. Yes it does hurt. Like you’re a flipping idiot if you are using your finger pads to pull burning plastic off of anything. But you spent a number of hours yesterday wrestling with the damn razor blade and nearly slicing your fingers open. Let’s keep going. Plus you might drip burning plastic on your face because you’re on your back under the damn wire you’re lighting on fire. On your boat, that should not catch on fire. I should go look for my leather gloves up in my truck in the parking lot, but I want to finish the damn project let’s just keep going. Jesus H Christ it hurts every time.
That all got a little stream-of-consciousness for a blog post, I know.
I resorted to soldering the wires. Upon review of my records, I have neglected to photograph the ugly result of my soldering. I will have to come back and add those images as comments.
So, stripping wires with a flame is good, but have a glove or something handy to pull off the insulation. I recommend soldering them together with appropriate heat shrinking.
In the end, the wires were so small and compact that I had a hard time melting heat shrink appropriately over each wire strand and I resorted to electrical tape. I may go back and re-do all of this at some point, but it works for the present.
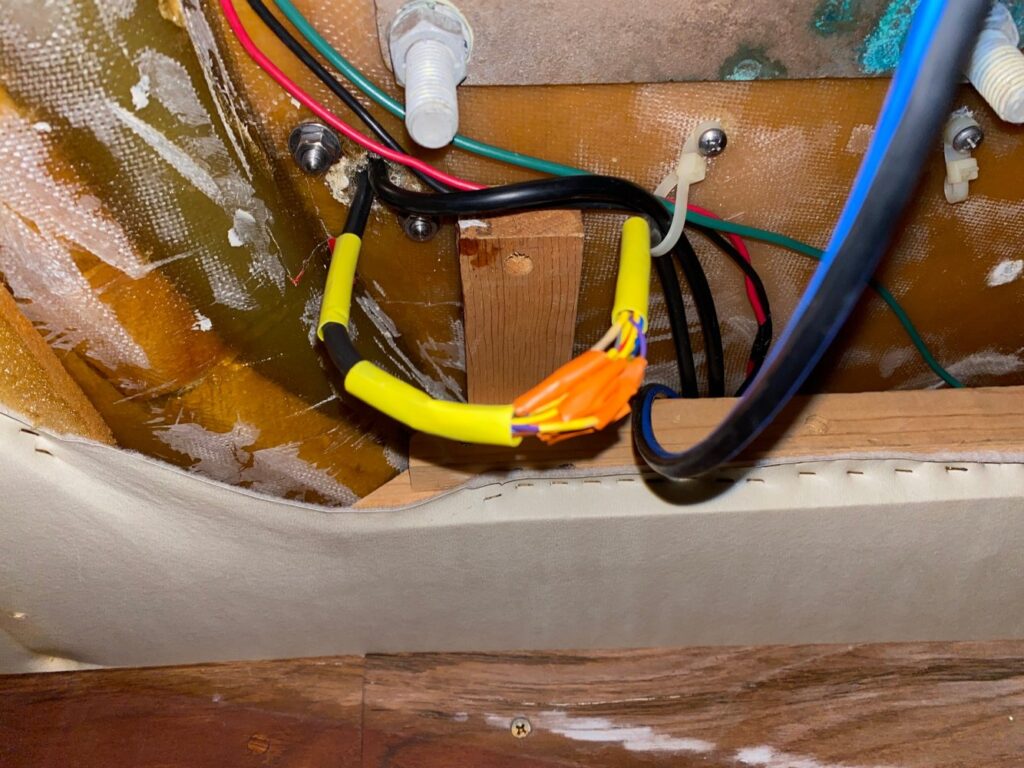